Making Bead Furnaces
Today was about preparing for another experiment in glass bead making next weekend at a local SCA event. The goal was to produce two cobb furnaces.
The process begins by slipping over to the neighbour's to borrow a bucket of horse manure. Thankfully the weather has been hot and dry the last day or two so it was easy to get some that was well dried and broke up easily. The first step is to break up the whole bucketful.
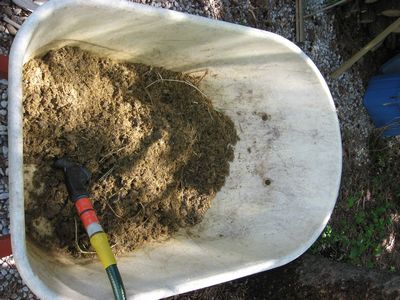
To this we add a bag of Ball Dark clay
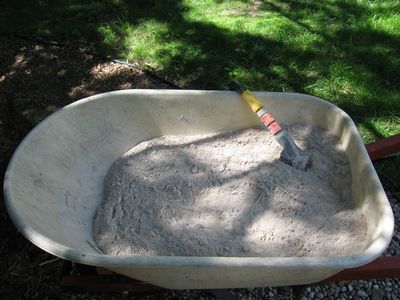
Stir well, add water, and just keep mixing until you have a good cobb to work with
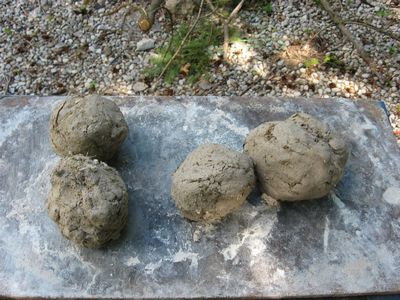
And hey presto out pops two furnaces
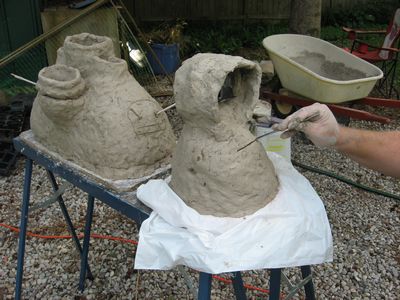
The one in the background is becoming a standard design for this work. The base is a 30x60cm oval matching one of the bases found at Ribe. This style can be set with two working ports - one on each short side. The port for the bellows is in the center of the long side. Opposite that port is a chute for loading charcoal currently blocked with a crucible for annealing. At the top are two chimneys with another pot for annealing between them.
Annealing is a problem we are working on and having two options to measure for temperature will allow us to explore some options. The crucible sitting in the side is one option we haven't tried before. The pot on top we have used before but this time I have made it deeper and thinned out the top of the furnace to increase the heat transmission. We will also try filling the pot with ash.
The furnace is the foreground is new for us. We nicknamed it the teapot when we tried it at the end of May. This design comes from Trine the beadmaker at Ribe and is similar to one she currently uses. It is based on a circular furnace base found at Ribe.
This furnace uses a burn chamber (the lower portion) and a small chimney at the top to allow the heat out. This chimney has a covered working area to allow the bead maker the work. On the side is the same charcoal chute (being cut out in the picture) and annealing crucible, and a port for the air from the bellows.
We played with a pure clay version of this furnace but had temperature control problems as the fresh clay broke down.
These two furnaces are built of cobb which will hold together better and are being let dry for a week before firing which will lead to a more stable furnace.
For both furnaces the upper surfaces are a guess as there are no archaeological remains I am aware of other than a few pieces of sintered cobb from Ribe that were found on top of one of the bases - that may be remains of the walls of a furnace.
Neil
The process begins by slipping over to the neighbour's to borrow a bucket of horse manure. Thankfully the weather has been hot and dry the last day or two so it was easy to get some that was well dried and broke up easily. The first step is to break up the whole bucketful.
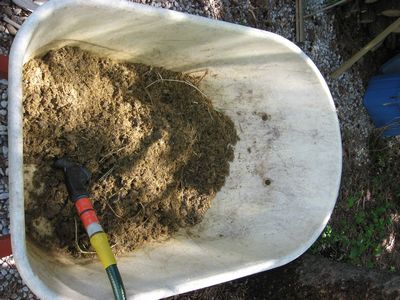
To this we add a bag of Ball Dark clay
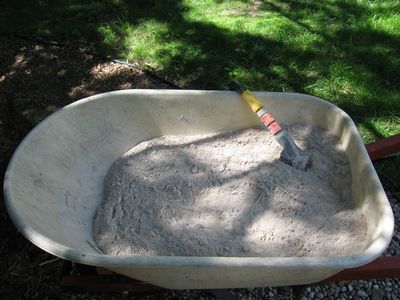
Stir well, add water, and just keep mixing until you have a good cobb to work with
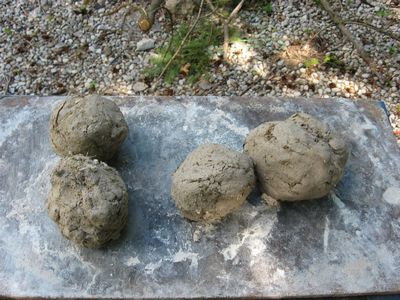
And hey presto out pops two furnaces
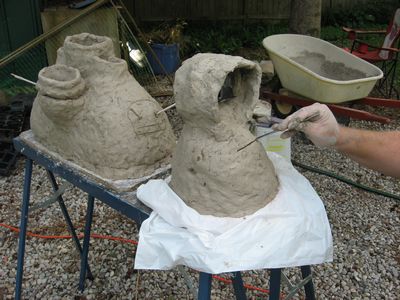
The one in the background is becoming a standard design for this work. The base is a 30x60cm oval matching one of the bases found at Ribe. This style can be set with two working ports - one on each short side. The port for the bellows is in the center of the long side. Opposite that port is a chute for loading charcoal currently blocked with a crucible for annealing. At the top are two chimneys with another pot for annealing between them.
Annealing is a problem we are working on and having two options to measure for temperature will allow us to explore some options. The crucible sitting in the side is one option we haven't tried before. The pot on top we have used before but this time I have made it deeper and thinned out the top of the furnace to increase the heat transmission. We will also try filling the pot with ash.
The furnace is the foreground is new for us. We nicknamed it the teapot when we tried it at the end of May. This design comes from Trine the beadmaker at Ribe and is similar to one she currently uses. It is based on a circular furnace base found at Ribe.
This furnace uses a burn chamber (the lower portion) and a small chimney at the top to allow the heat out. This chimney has a covered working area to allow the bead maker the work. On the side is the same charcoal chute (being cut out in the picture) and annealing crucible, and a port for the air from the bellows.
We played with a pure clay version of this furnace but had temperature control problems as the fresh clay broke down.
These two furnaces are built of cobb which will hold together better and are being let dry for a week before firing which will lead to a more stable furnace.
For both furnaces the upper surfaces are a guess as there are no archaeological remains I am aware of other than a few pieces of sintered cobb from Ribe that were found on top of one of the bases - that may be remains of the walls of a furnace.
Neil
Labels: glass beads
0 Comments:
Post a Comment
<< Home