Gas Jet Bead Furnace MK 3
(cross posted from 'Hammered Out Bits')
... referred to (why?) by Neil and Jean as the 'tea pot' style.
{ed.Karen: because it looks like a teapot:) }
About the time Neil Peterson got seriously interested in compiling tables detailing just what forms, colours and shapes were common during the Viking Age, I had been introduced to the modern methods of making lampwork beads. At Dan Nickels' 'Folly in the Forge' workshop, a local glass bead maker had demonstrated the basic technique. Along with fellow blacksmiths David Robertson and Janis Book, some basic supplies and Corina Tettinger's (excellent) manual 'Passing the Flame' were purchased. Over the next several months, I had made about 100 beads using my oxy-propane torches, gaining at least a basic understanding of how tohandle hot glass in rod form.
Neil's experiments proceeded with a furnace based on the base plate remains from Ribe, Denmark, with a superstructure suggested by traditional Indian models. These used a dome like enclosure, with small working ports into the interior to contain the required heat. The glass would be manipulated inside the furnace through these ports. Neil is now working his fifth version based on this system.
In spring 2008, I had a chance to meet with Trene Theut, an artisan interpreter at the Ribe Viking Centre, and its glass bead specialist. At that meet, Trene described her most recent experimental furnace. The next day I was able to see this furnace on my visit to the site itself.
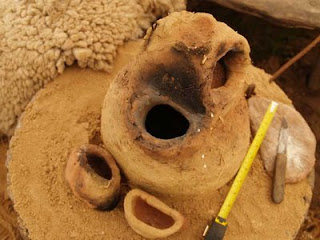
(Trene's Experimental Gas Jet Furnace at the Ribe Viking Centre)
The initial concept behind Trene's set up was to trap and utilize the hot gasses from the charcoal fire, rather than work inside the furnace itself. The combustion gasses escaped from small vent in the top of the roughly cylindrical clay structure. In this way the manipulation of the glass was physically more like working with a modern torch flame.
Although not designed specifically for this method, those working with Neil's 'oven' design, more and more were found to manipulate the glass in the 'chimney' holes in the top of the structure. (See Video Segment)
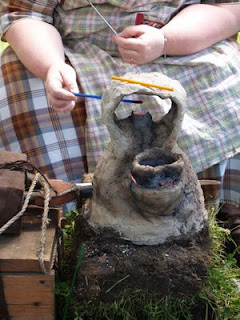
(Mark 2 'Teapot' Gas Jet Furnace in use)
To that end, a first attempt at a building a specifically gas jet furnace was undertaken at the July Trillium War demonstration. This specific layout was quickly found to be quite unsuccessful, as the upper gas jet never produced enough heat to do much more than slump the glass rods used as a raw material.
Taking a close look at Neil's first rendition of the system, I thought I could apply some of my experience with charcoal fired forges to the design.
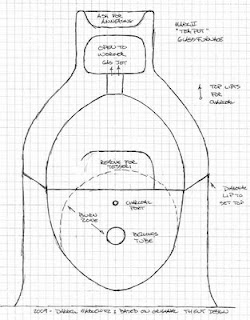
(Theoretical Gas Jet Bead Furnace - scale 1:2)
One of the biggest problems with the Mark 2 layout was found to be the sloppy fit between the large side loading port and the inserted annealing cup. The large gaps here were found to be venting as much (if not more) of the hot combustion gasses as the top working vent. One of the largest changes in the new furnace is that instead of a side loading port for charcoal, it is designed in two sections so that the entire top can be lifted off to add fuel. The top rim of the lower section is beveled, so that the upper body would quickly slide back to the correct location when it was replaced after loading.
A second major modification, is the change in the shape of the lower section of the furnace. Rather than an elongated D cross section, this proposed furnace is more of an 0 shape. The bellows tube is placed so that the distance below the furnace is roughly equal to the side to side measurement. This will allow the air blast to completely penetrate the charcoal mass, as well as cause any piled fuel to move down and into the air blast as it is consumed. A small hole into the interior, located roughly two inches above the bellows tube opening, would allow the operator to directly observe when the top of the charcoal had dropped to a level where addition was necessary.
In this arrangement, the bead maker sits directly opposite the bellows. There would be a small port with replaceable cover at the middle level of the side wall, allowing working of tesseri inside the furnace itself. (This using the method discovered at the Trillium demo, detailed in an earlier posting.)
Most of the detailed glass work is intended to take place in a second small chamber placed at the top of the furnace, directly over the exhaust port for the combustion gasses. This would have a single small opening, placed on the side closest to the glass worker. The very top of the furnace would have a shallow cup, intended to be filled with ashes to provide an annealing area headed from below.
With luck a first prototype of this modified furnace - MK 3 - will be built and tested later in July.
(Darrell)
... referred to (why?) by Neil and Jean as the 'tea pot' style.
{ed.Karen: because it looks like a teapot:) }
About the time Neil Peterson got seriously interested in compiling tables detailing just what forms, colours and shapes were common during the Viking Age, I had been introduced to the modern methods of making lampwork beads. At Dan Nickels' 'Folly in the Forge' workshop, a local glass bead maker had demonstrated the basic technique. Along with fellow blacksmiths David Robertson and Janis Book, some basic supplies and Corina Tettinger's (excellent) manual 'Passing the Flame' were purchased. Over the next several months, I had made about 100 beads using my oxy-propane torches, gaining at least a basic understanding of how tohandle hot glass in rod form.
Neil's experiments proceeded with a furnace based on the base plate remains from Ribe, Denmark, with a superstructure suggested by traditional Indian models. These used a dome like enclosure, with small working ports into the interior to contain the required heat. The glass would be manipulated inside the furnace through these ports. Neil is now working his fifth version based on this system.
In spring 2008, I had a chance to meet with Trene Theut, an artisan interpreter at the Ribe Viking Centre, and its glass bead specialist. At that meet, Trene described her most recent experimental furnace. The next day I was able to see this furnace on my visit to the site itself.
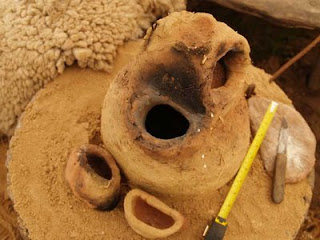
The initial concept behind Trene's set up was to trap and utilize the hot gasses from the charcoal fire, rather than work inside the furnace itself. The combustion gasses escaped from small vent in the top of the roughly cylindrical clay structure. In this way the manipulation of the glass was physically more like working with a modern torch flame.
Although not designed specifically for this method, those working with Neil's 'oven' design, more and more were found to manipulate the glass in the 'chimney' holes in the top of the structure. (See Video Segment)
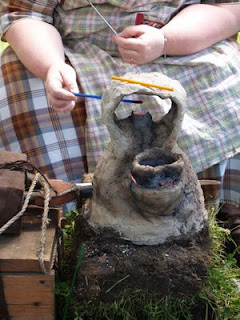
To that end, a first attempt at a building a specifically gas jet furnace was undertaken at the July Trillium War demonstration. This specific layout was quickly found to be quite unsuccessful, as the upper gas jet never produced enough heat to do much more than slump the glass rods used as a raw material.
Taking a close look at Neil's first rendition of the system, I thought I could apply some of my experience with charcoal fired forges to the design.
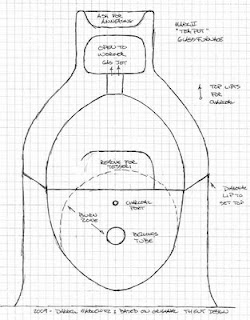
One of the biggest problems with the Mark 2 layout was found to be the sloppy fit between the large side loading port and the inserted annealing cup. The large gaps here were found to be venting as much (if not more) of the hot combustion gasses as the top working vent. One of the largest changes in the new furnace is that instead of a side loading port for charcoal, it is designed in two sections so that the entire top can be lifted off to add fuel. The top rim of the lower section is beveled, so that the upper body would quickly slide back to the correct location when it was replaced after loading.
A second major modification, is the change in the shape of the lower section of the furnace. Rather than an elongated D cross section, this proposed furnace is more of an 0 shape. The bellows tube is placed so that the distance below the furnace is roughly equal to the side to side measurement. This will allow the air blast to completely penetrate the charcoal mass, as well as cause any piled fuel to move down and into the air blast as it is consumed. A small hole into the interior, located roughly two inches above the bellows tube opening, would allow the operator to directly observe when the top of the charcoal had dropped to a level where addition was necessary.
In this arrangement, the bead maker sits directly opposite the bellows. There would be a small port with replaceable cover at the middle level of the side wall, allowing working of tesseri inside the furnace itself. (This using the method discovered at the Trillium demo, detailed in an earlier posting.)
Most of the detailed glass work is intended to take place in a second small chamber placed at the top of the furnace, directly over the exhaust port for the combustion gasses. This would have a single small opening, placed on the side closest to the glass worker. The very top of the furnace would have a shallow cup, intended to be filled with ashes to provide an annealing area headed from below.
With luck a first prototype of this modified furnace - MK 3 - will be built and tested later in July.
(Darrell)
Labels: glass beads
0 Comments:
Post a Comment
<< Home