Iron consolidation weekend - Jan 2005
Beating the Bloom
We gathered on a chilly January day to try beating the blooms we had down into bars.
The Team:
Leader |
Darrell Markewitz |
Staff |
Ken Cook Gustof |
Recorder |
Neil Peterson |
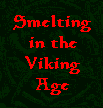 |
Reports of all of our iron smelting efforts along with more articles and information are available on the "Iron Smelting in the Viking Age" CD from the Wareham Forge. Copies of the CD can be purchased here. |
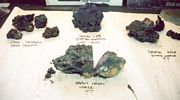 |
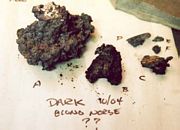 |
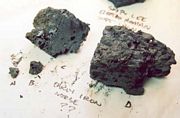 |
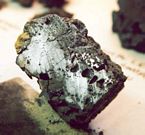 |
Available were materials from four different smelts |
DARC EconoNorse - 6 pieces A: 1.66 Kg, 300 cm3 B: 250g C,D,E,F: 100 g |
Markewitz Norse - 4 pieces A&B: c. 20g C: 1.025 Kg D: 1.84 Kg |
Markewitz Norse - Piece D A look at the glassy slag with iron appearing in the top right. |
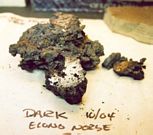 |
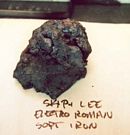 |
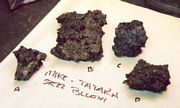 |
|
Part of the cut on the DARC bloom. Nice shiny metal. |
Sauder & Williams ElectroRoman 3.3 Kg, 600 cm3 |
McCarthy Tatara - four pieces A: 150g, 50 cm3 B: 1 Kg, 100 cm3 C: 325g, 75 cm3 D 220g |
On examining the materials available the following decisions were made:
McCarthy Tatara - On examination of the four pieces: one had a visible 'bright'
colour (after quenching) suggesting a high carbon content, two had a lighter,
more spongey texture, and the last one was more condensed It was decided to use
this more condensed fragment for the day's work. As other pieces from this smelt
had been successfully consolidated to workable bar by others (at the Early Iron
Symposium) it was further decided to work this piece first.
Sauder & Williams ElectroRoman This material was only one section of a much larger
bloom. It was already partially consolidated. Because of the density and size,
it was decided to leave working this bloom to a later time.
Markewitz Norse - On examining the new section, along with the surface appearance
of the first section (by Elizabeth Hendrix) it was decided not to further work
this bloom. The iron is very light and bubbly - and shows a clear formation around
the edges of charcoal pieces embedded. The majority of the material also is composed
of a solid mass of slag at the lower 2/3 of the piece. It was felt this bloom
is better retained as is for research / education.
DARC EconoNorse - Material from this smelt was the primary focus of the team.
It was decided to retain the smaller section for future study and reference. The
larger piece would be worked in the forge.
Progress of Work: (only briefly covered here)
1. Each piece was dried (from volume measurement) on top of the wood stove |
|
2. The piece was pre heated in the gas forge. The top temperature reached
was a medium to bright orange. |
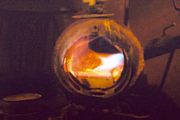 |
3. At this point the piece was transfered into a coal forge |
|
4. Primary compacting was done with a hand hammer, the material at a yellow
through orange heat. This stage mainly consisted of collapsing voids and
working any surface fragments into the centre. |
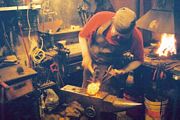 |
5. Care was taken to gather any fragments that broke off that were much
bigger than peanut sized. |
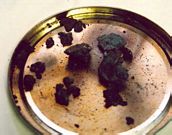 |
6. The roughly egg shaped piece was now compressed towards a rectangular
profile. This was done via two strikers (with about 5 lb hammers) using
light strokes. The individual imacts were directed by the strikers - collapsing
material that stood up from the surface. The block was constantly rotated
to all sides. |
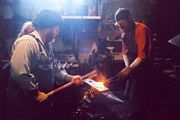
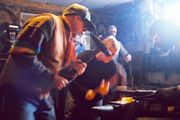 |
7. During this process, several courses of welding were undertaken. This
was done with the hand hammer to allow for diagonal strokes. These functioned
to seal the many diagonal cracks within the material. |
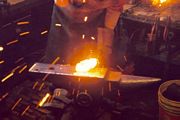 |
8. Once the block was roughly rectangular and mostly compressed, a more
standard series of forge welds were taken on each of the six sides using
the hand hammer. |
|
9. To spead the process, next the block was drawn under the air hammer.
Each forging step started at a welding heat. |
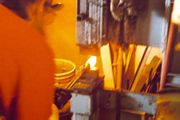 |
10. The block was drawn to roughly 7 inches long by 1/2 thick by about
1 1/2 wide. |
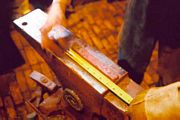 |
11. The block was nicked with a hot set at the mid line and folded. Borax
flux was used. The block was then forge welded, again a standard weld with
the hand hammer. |
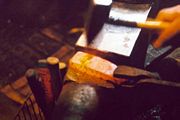 |
13. The block was trimmed to shape with the hand hammer, and left to air
cool. Latter spark testing would suggest the metal has a mid level carbon
content. |
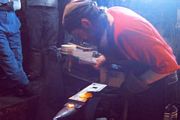
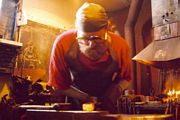 |
The bar still warm showing the weld |
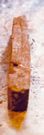 |
The finished bar |
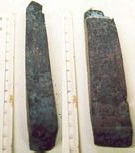 |
The slag ring from the bottom of the forge |
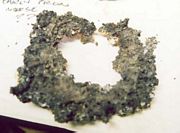 |
Having established some feel for the process of consolidating a bloom, the team
prepared to work the bloom from the DARC EconoNorse smelt. After a short coffee
break, a fresh coal fire was started. Tasks were re-assigned. The piece to be
worked was roughly three times the size of that from the first sequence. A similar
sequence of actions was followed:
- Drying
- Pre-heat
- Transfer to coal forge
- Under the work of the hand hammer, during the very first heat, it was noticed
that a large volume of very liquid. glassy slag was squirting out from the
interior. This would usually be accompanied by a fragment of bloom cracking
away. On the second or third heat, the mass split into three larger fragments.
Large deposits of slag were clearly visible on the interior surfaces. On the
bloom, one section that was roughly circular and slightly flattened had stood
up off the surface of the mass. When hammered, this section was obviously
more compressed to start with (from an attempt to consolidate the mass after
extraction from the smelter ??). Deemed 'the puck', it was decided to progress
with this piece of the bloom and set the others aside for later work.
- As with the first sequence, this material was worked with the hand hammer.
The mass was compressed to the centre, strokes aimed so to fold individual
pieces together. Generally this was done at a yellow heat, although several
welding heats were also taken. The results here were quite different than
the first sequence. The material collapsed quickly, but continuted to fracture.
No modification in hammer stokes or working temperatures seemed to prevent
this. The end result was a cluster of peanut to half walnut sized fragments
with irregular edges.
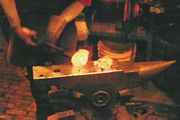 |
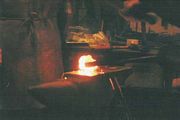 |
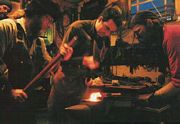 |
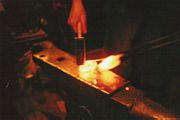 |
Bloom on anvil |
Another side |
Ken & Gus hammer |
Shaping the bar |
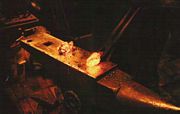 |
| | |
Examining the bar |
- The appearance of the cooled fragments, as well as their action under the
hammer suggested that this material might in fact be a high carbon 'cast'
iron. One fragment was water cooled and spark tested against a known piece
of modern cast iron. The sparks were almost identical. An image of the fragments
produced in this sequence, shown against their relative positions on the starting
bloom, can be seen at: here
Conclusions
- The team was able to establish a rough process for consolidating a smelted
bloom mass into a working bar of metal. (It is noted that this was related
to smaller fragments, with existing equipment suited to pieces no larger than
roughly 6 x 6 x 4 inches.) It was also understood that a large number of more
modern technologies were employed. Further experiments and practical experience
must be gathered towards using Viking Age tools and equipment for the consolidation
process.
- It was obvious that although the DARC smelt of 10/23/04 had resulted in
a metallic bloom, this mass proved have too high a carbon content to allow
it to be consolidated into a workable iron bar. Obviously closer examination
has to be made into the carbon control phase of the smelting process. Historically
a 'failed bloom' such as was produced at the last smelt would have been smashed
to fragments and re-processed to lower its carbon content. For the purposes
of our experimental sequence, it was decided that the fragments on hand would
be retained for further study and documentation.
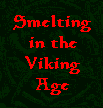 |
Reports of all of our iron smelting efforts along with more articles and information are available on the "Iron Smelting in the Viking Age" CD from the Wareham Forge. Copies of the CD can be purchased here. |