Iron Production Experiment - June 2005
Date: 11 June, 2005
Location: Vinderheima
Premise: All proper equipment, done in costume. A test run for the presentation
at CANIRON 2005.
Experiment Notes - Norse Short Shaft Smelter
The Team:
Leader |
Darrell Markewitz |
Staff |
Kevin Jarbeau / Dave Cox |
Recorder |
Neil &Karen Peterson |
Charcoal Monkey |
Ken Cook |
Animal Wrangler |
Vandy Simpson |
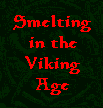 |
Reports of all of our iron smelting efforts along with more articles and information are available on the "Iron Smelting in the Viking Age" CD from the Wareham Forge. Copies of the CD can be purchased here. |
Setting up the smelter:
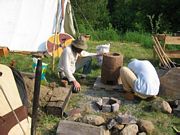 |
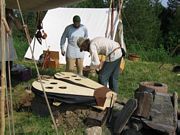 |
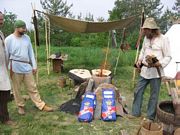 |
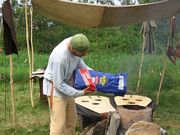 |
Overview |
Locking the bellows |
For our friends at Royal Oak |
One more for Royal Oak |
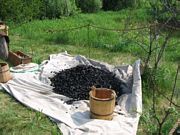 |
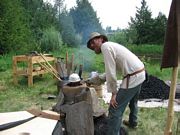 |
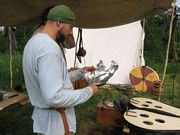 |
|
150 lbs of charcoal |
Jiffy-pop |
Smelter Corn! |
Time |
Event |
Measures |
Relative |
Absolute |
Total |
Relative |
Elapsed |
Charcoal |
Ore |
0:00 |
00 |
addition rough charcoal, gentle air blast |
|
|
|
|
0:33 |
33 |
first measured charcoal |
1 |
4 lbs* |
4 lbs |
|
0:44 |
11 |
charcoal |
2 |
|
8 lbs |
|
0:59 |
15 |
charcoal |
3 |
|
12 lbs |
|
1:09 |
|
seed charge |
1 |
.75 lbs* |
|
.75 lbs |
1:16 |
17 |
charcoal |
4 |
|
16 lbs |
|
1:26 |
16 |
seed charge |
2 |
.75 lbs |
|
1.5 lbs |
1:34 |
12 |
charcoal |
5 |
|
20 lbs |
|
1:42 |
16 |
seed charge |
3 |
.75 lbs |
|
2.25 lbs |
1:50 |
16 |
charcoal |
6 |
|
24 lbs |
|
1:59 |
17 |
seed charge |
4 |
.75 lbs |
|
3 lbs |
2:08 |
18 |
charcoal |
7 |
|
28 lbs |
|
2:24 |
25 |
seed charge |
5 |
.75 lbs |
|
3.75 lbs |
2:27 |
19 |
charcoal |
8 |
|
32 lbs |
|
2:33 |
|
switch to electric blower - rate at D (815 L/M) |
|
|
|
|
2:37 |
10 |
charcoal |
9 |
|
36 lbs |
|
2:47 |
10 |
charcoal |
10 |
|
40 lbs |
|
23 |
full charge |
6 |
1.5 lbs |
|
5.25 lbs |
2:56 |
9 |
charcoal |
11 |
|
44 lbs |
|
full charge |
7 |
1.5 lbs |
|
6.75 lbs |
|
air rate at B+ (625 L/M ) |
|
|
|
|
3:08 |
12 |
charcoal |
12 |
|
48 lbs |
|
half charge |
8 |
.75 lbs |
|
7.5 lbs |
3:19 |
9 |
charcoal |
13 |
|
52 lbs |
|
full charge |
9 |
1.5 lbs |
|
9 lbs |
3:24 |
|
slag tap |
|
|
|
|
3:31 |
12 |
charcoal |
14 |
|
56 lbs |
|
full charge |
10 |
2.25 lbs |
|
11.25 lbs |
3:41 |
10 |
charcoal |
15 |
|
60 lbs |
|
full charge |
11 |
2.25 lb |
|
13.5 |
3:50 |
26 |
slag tap |
|
|
|
|
3:53 |
12 |
charcoal |
16 |
|
64 lbs |
|
full charge |
12 |
2.25 lbs |
|
15.75 lbs |
4:04 |
11 |
charcoal |
17 |
|
68 lbs |
|
full charge |
13 |
1.5 lbs |
|
17.25 lbs |
4:16 |
12 |
charcoal |
18 |
|
72 lbs |
|
full charge |
14 |
3 lbs |
|
20.25 lbs |
4:33 |
17 |
charcoal |
19 |
|
76 lbs |
|
full charge |
15 |
3 lbs |
|
23.25 lbs |
4:46 |
13 |
charcoal |
20 |
|
80 lbs |
|
half charge |
16 |
.75 lbs |
|
24 lbs |
4:59 |
13 |
charcoal |
21 |
|
84 lbs |
|
|
begin burn down phase |
|
|
|
|
5:17 |
|
air flow reduced to minimal - remaining charcoal removed |
|
|
|
|
5:28 |
|
bloom removed |
|
|
|
|
NOTES:
Charge times recorded at END of unit addtition
* All charcoal charges are based on a 'standard pail' -
weight of 4 lbs
All ore charges are based on a 'standard scoop' - weight of 3/4 lbs
Estimated from known marks
YIELD: 7 lbs (estimated)
About 30% return on ore weight
Some photos of the norse boys working the bellows.
Notice the two different ways to use the pit.
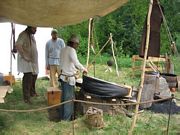 |
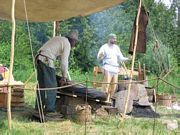 |
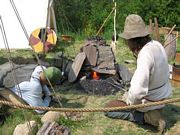 |
|
Ketill in pit |
Ketill standing tall |
Slag Running |
As the temperature was in the "very high" range we aborted the use of the bellows part way in.
consolidating the bloom
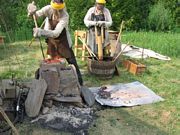 |
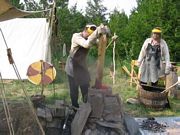 |
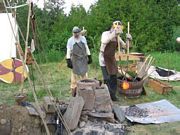 |
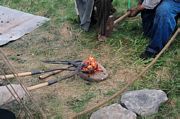 |
Shove out charcoal |
Thumping |
Removing the bloom |
First strike |
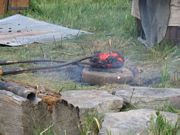 |
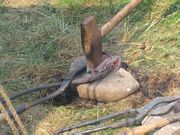 |
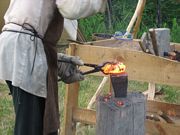 |
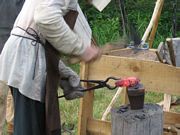 |
Flattened Bloom |
More consolodation |
Hand finishing |
A little more |
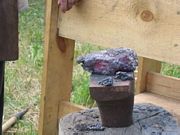 |
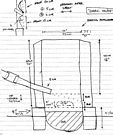 |
| |
Bloom cooling |
Measurements |
We also used this smelt as an opportunity to test presentation techniques
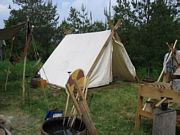 |
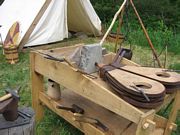 |
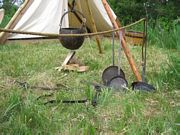 |
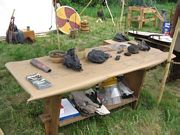 |
Tent |
Forge Table |
Finished iron |
Info table |
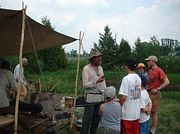 |
| | |
Talking to public |
It was too damn hot!
As a seasonal activity, our feeling is that iron smelting would be
undertaken (with good reason) in late fall if not early winter. Slaves
are indicated for the labour.
The new bellows was finished up at about 5 pm Friday. Then work was
started on the smelter - untill it got too dark to see. This was
finished up the next morning. With adding all the set up for the
presentation, we were about ready to start the pre-heat at just after
10 am - not too much after schedule. By that time it was already
pushing 30 degrees!
The split wood preheat ran for about an hour. Started in with full
charcoal and bellows work at about 11:30 (although the "clock" as usual was reset to 1200h). We were measuring shifts on
the bellows using the water jar, on a 6 minute rotation. After about
two hours, we started to realize that we were going to kill ourselves.
Kevin was by far the best on the bellows action, Dave had the
muscle to manage, and Darrell was just managing to hang in there. A command
decision was made, and we switched to the electric blower at 2 1/2
hours into the smelt. As we were getting ready, we let a number of our
DARC support team try a shift on the bellows - I don't think any of
them wanted a second shift on it.
We did leave the belows out for the public to try. None of them would
work it even a good part of a 6 minute shift by the water jar!
We did set the blower rate to roughly the same volume (by sound) as the
bellows was producing. This gave us and end result that would have been
approximately the same.
The initial consolidation, done just as the bloom was extracted,
proceeded extremely well, Some fragmentation from the primary mass
ocurred, but a good sized block was forming up. A second consolidation
was done, using the smelter with extra charcoal added as a giant forge.
Dave and Ken on the sledge hammers were quite effective. On the third
heat, everyones attention slipped. The bloom ended up moving right up
against the air blast - and we effectively overheated and
burned the metal. In our estimation, we not only ruined the surface,
but also lost about 1/3 of our mass. Very bad.
The end product is a block of metal about 6 long by 3 wide by 2 thick
with ragged edges. Total wieght at this point is about 2 3/4 lbs.
What we learned
The biggest thing was we learned to judge the activity of the smelter
by sound alone.
The smelter itself is effective in design - but requires a shallow pit
below it to provide the required insulation at the base. The
construction should allow for at least a second use with some internal
patching. It cannot be moved after the first use however. (A new
smelter will have to be built for CANIRON)
The bellows should provide enough air to complete the reaction
effectively. The bellows action requires too much effort to operate
(especially in plus 30 temps!). A number of modifications have been
suggested, including rigid internal hoops and altering the top plate
shape. There is some question about enlarging the tuyere diameter, this
requires some more research.
As was estimated, there is a bottom end to the physical reaction, in
terms of a minimum amount of ore required before any bloom can form. We
likely were pretty close to this bottom limit at 20 lbs ore. The size
of bloom we produced compares with archaeological samples.
It was generally agreed that if we had extracted the small bloom, then
added a bucket of charcoal and used the smelter as a forge for two or
three consolidation heats, the mass of the smelter would have remained
hot enough to then proceed with a second smelt. Historically, this
would allow for a couple of smaller and more easily managed blooms to
have been produced in series, rather than one large bloom (more typical
of modern experiments).
Discussion was made of holding a smelt in late October (schedule
permitting). The experiment objective would be to test out this last
idea, running a 'two bloom' smelt over a period of roughly 8 hours.
[In fact we ran a single bloom smelt in the same smelter in early Novermeber -- see
here for details]
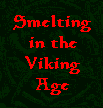 |
Reports of all of our iron smelting efforts along with more articles and information are available on the "Iron Smelting in the Viking Age" CD from the Wareham Forge. Copies of the CD can be purchased here. |