Iron Production Experiment - May 2002
Date: 25, 26 May, 2002
Location: Vinderheima
Premise: If they made iron -- then so can
we using the same techniques
Conclusion: We can't do it this way
The Team:
Staff |
Kevin Val Dave Kevin Gus |
Recorder |
Neil Peterson |
Leader |
Darrell Markewitz |
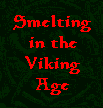 |
Reports of all of our iron smelting efforts along with more articles and information are available on the "Iron Smelting in the Viking Age" CD from the Wareham Forge. Copies of the CD can be purchased here. |
Starting Facts
Smelter
The experiment began with the creation of a smelter. The smelter was
created using local slab rock and was 38 cm from the "back right" to
"front left" corners by 43 cm across the other diagonal and
approximately 38 cm deep. The corners of the smelter were caulked using
a local clay. A hole was left for the bellows pipe in the front face.
This opening is approximately 2.5 cm by 5 cm.
Charcoal
Many bags of "Royal Oak" charcoal were purchased. This charcoal was
then broken up to a rough standard size of 127 cm
3.
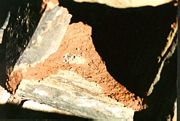 |
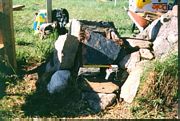 |
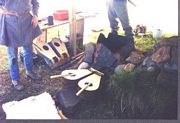 |
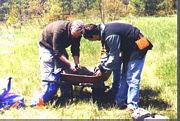 |
Looking down into the smelter |
The outside of the smelter |
The smelter with bellows set up |
Breaking Charcoal |
Ore
A total of 6 Kg of ore was needed for this experiment. Unfortunately we
did not have that much "single source" ore available. The "ore" for
this experiment came from two sources:
- 4.8 Kg of Ore from L'anse aux Meadows (mostly 1cm size) [FeO3
6x% + Si + H2O]
- Forge scale (flake size 2-3mm) ["pure" FeO2]
Bellows
The bellows were constructed on the day of the experiment. Following
the smelting it was determined that each single "pump" of one side of
the bellows produced between 2.4 and 2.9 litres of air. The rhythm used
in pumping the bellows averaged 63 beats per minute. An average volume
of 2.8 L of air per minute is assumed.
Measurements
Care was taken in the measurements used in this page but some margin of
error does exist. Especially in the conversions between imperial and
metric units. Chemical analysis performed by Marcus Burnham. These analyses can therefore be considered
totally accurate.
Roasting the Ore.
This was accomplished using two propane forges. The
first employed a can containing approximately 460 cubic cm of ore in a
layer 3 cm thick. The second employed a flat pan with a layer 1 cm
thick. The can roasted a batch of ore approximately every 15 minutes. The pan was much faster averaging 3 minutes per
batch. The roasted ore was weighed at 2.95 Kg. The weight
being reduced by 38.5% matches well with the analysed water content of
the ore being removed. Two samples of the ore (approx. 0.025 Kg each) were
removed for analysis. A lot of discussion occured about the best way to
accomplish the roasting. The small size of the ore grains led to a fair bit
of dust also being lost. Compare the colour of the unroasted (in can) and
roasted (in pan) ore.
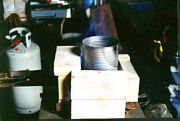 |
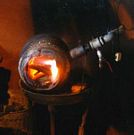 |
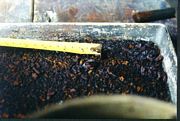 |
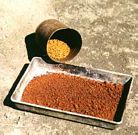 |
Roasting Can of Ore |
Roasting pan of Ore |
Pan of roasted ore |
Roasted and unroasted |
Preparing the "charges"
Due to the low silicon level in the ore used it was mixed with sand. The ore was split into three sections.
- 0.9 Kg was mixed with 0.1 Kg of sand. This is refered
to later as the "carbon charge" or "third charge"
- 1.8 Kg was mixed with 0.2 Kg of sand. This is refered
to later as the "second charge"
- The remaining 0.2 Kg was mixed with 0.7 Kg of sand. An
additional 2.4 kg of furnace scale was added. This is refered to later
as the "first charge".
Heating the smelter
Absolute Time |
Elapsed Time |
Notes |
1225h |
0 |
A small wood fire was lit in the smelter to begin
slowly heating it and drying the clay caulking |
1350h |
T+1:25 |
The smelter was filled with charcoal and the
bellows were brought into use to begin heating the smelter to operating
temperature |
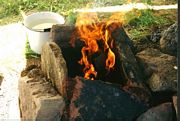 |
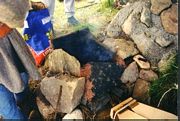 |
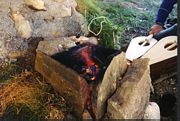 |
|
Small wood fire |
Charcoal fill |
Adding air |
Smelting the ore
Absolute Time |
Elapsed Time |
Notes |
1441h |
T+2:16 |
The "first charge" was placed on a board in the
smelter which was then "topped up" with approximately 4 kg of charcoal |
1503h |
T+2:38 |
A problem with the bellows caused the air flow to be stopped |
1511h |
T+2:46 |
Bellows air flow resumed |
1520h |
T+2:55 |
A sample of the slag was removed by inserting and removing a 0.6 cm iron rod |
1544h |
T+3:19 |
The smelter was topped up with charcoal |
1558h |
T+3:33 |
Bellows stopped and the second charge was placed in the
smelter on a board. The smelter was again topped up with charcoal and
pumping was resumed on the bellows |
1628h |
T+4:03 |
The smelter was topped up with charcoal |
1650h |
T+4:35 |
The smelter was topped up with charcoal |
1708h |
T+4:53 |
The smelter was topped up with charcoal |
1732h |
T+5:17 |
The smelter was topped up with charcoal |
1808h |
T+5:53 |
Bellows stopped and the third charge was placed in the smelter. The smelter was again topped up with charcoal and pumping was resumed on the bellows |
1835h |
T+6:20 |
The smelter was topped up with charcoal |
1916h |
T+7:01 |
Bellows stopped and the charcoal was scraped away for a short investigation |
1921h |
T+7:06 |
Bellows restarted |
1926h |
T+7:11 |
The smelter was topped up with charcoal |
2013h |
T+7:58 |
Bellows stopped and the smelter was broken open and examined |
0900h |
T+20:35 |
Final "excavation" of the smelter |
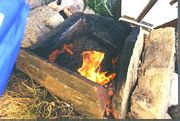 |
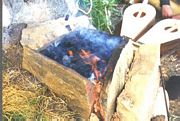 |
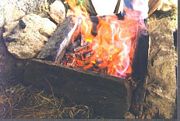 |
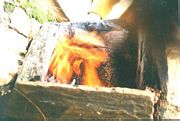 |
First charge |
First charge |
Fire pattern |
Second charge |
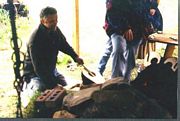 |
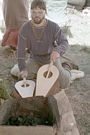 |
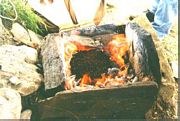 |
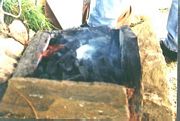 |
Kevin Smith |
Val on bellows |
Third charge |
Third charge |
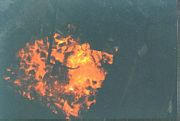 |
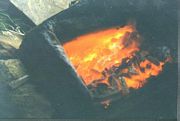 |
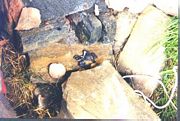 |
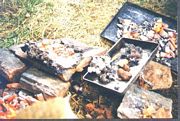 |
Coals burning |
Coals burning |
Slag leaking out |
Groupings of slag |
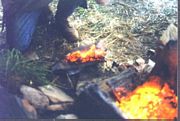 |
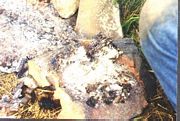 |
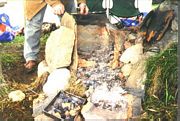 |
|
Slag on the rocks |
Cooled slag |
Open smelter |
Examining the results
Measurement |
Note |
22 Kg |
Total charcoal used |
0.77 Kg |
Metallic (magnetic) slag removed from above blob |
0.45 Kg |
Slag removed from above main blob |
3.04 Kg |
Main slag blob removed |
0.97 Kg |
Magnetic material fron base ash (very small grain size) |
1.02 Kg |
Non-magnetic material from base ash - including paper scraps |
0.57 Kg |
Slag removed from front furnace rock above air hole |
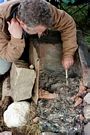 |
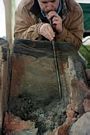 |
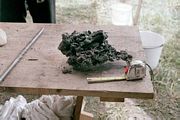 |
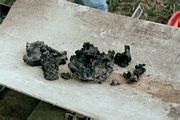 |
Excavating |
Blowing off ash |
Slag |
Slag pieces |
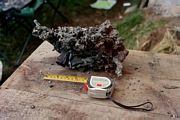 |
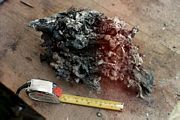 |
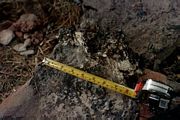 |
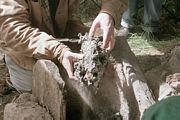 |
Slag |
Slag |
Slag bowl |
Removing bowl |
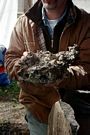 |
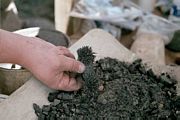 |
| |
Slag bowl |
Magnetic bits |
Results
We did not find an iron bloom.
Chemical Analysis
Analysis performed by Marcus Burnham
The compositions of the starting
materials for the first
Iron Smelting Weekend are shown in Table 1. Separate
analyses of the total major elements, ferrous iron, and
carbon and sulphur were carried out at the Ontario Geoscience
Laboratories of
the Ontario Geological Survey using X-ray fluorescence, iron
titrimetry, and combustion
infra-red analysis.
The
sample material was “bog ore” obtained from a site
close
to the historic site at L’Anse aux Meadows, Newfoundland. The material contained a
number of discrete
components, including aggregated clumps, tubular fragments, and fine
powder. In order to
determine how the
chemistry varied between the different components, an analysis of the
average
composition was accompanied by separate analyses were carried out on
sub-samples of separated “tubes” and
“chunks”.
|
Averaage
|
Tubes
|
Chunks
|
SiO2
|
2.24
|
1.76
|
3.23
|
TiO2
|
0.02
|
0.04
|
0.02
|
Al2O3
|
3.35
|
3.66
|
2.38
|
Fe2O3
|
66.53
|
60.98
|
66.07
|
FeO
|
2.49
|
2.56
|
1.38
|
MnO
|
0.62
|
1.15
|
1.45
|
MgO
|
0.08
|
0.09
|
0.05
|
CaO
|
0.69
|
1.05
|
0.75
|
Na2O
|
N.D.
|
N.D.
|
N.D.
|
K2O
|
0.02
|
0.03
|
0.02
|
P2O5
|
0.12
|
0.16
|
0.09
|
CO2
|
13.7
|
18.7
|
14
|
H2O
|
12.63
|
12.38
|
11.94
|
Table
1:
Major element compositions of bog
ore collected from close to the L’Anse aux Meadows historic site.
The results of the analyses indicate that the bog ore is
composed primarily of iron oxy-hydroxides, most likely limonite and/or
and goetite (FeOOH), with minimal ferrous (reduced) iron and very low
silica contents. All components of the ore
appear to be relatively carbon-rich (most likely present as calcium
and/or iron carbonate cement between grains in the chunks and tubes).
Conclusions & next steps
- The furnace scale was too small a size. It settled to the bottom without having a chance to melt
- Next time we use a single source of ore in a large "chunk" size
We revisited this smelter two years later and took the following pictures showing how it weathered.
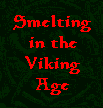 |
Reports of all of our iron smelting efforts along with more articles and information are available on the "Iron Smelting in the Viking Age" CD from the Wareham Forge. Copies of the CD can be purchased here. |